INFORMATION DU 24/04/2024
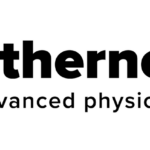
Ethernet APL : Ethernet to the field
Process plants today compete to produce more product with less waste. The digital transformation motivates C-Level executives to invest in more plant data coming from process automation systems and instrumentation.
Ethernet APL is a standardized Ethernet Advanced Physical Layer which meets all the requirements for the field of process plants.
Caracteristic
- 1000 m Cable Length
- 2 – Wire with Power
- Design for intrincic Safety
- Reuse existing cable
- Enable Field Instruents woith Ethernet
Ethernet APL is the ruggedized, two-wire, loop-powered Ethernet physical layer that uses 10BASE-T1L plus extensions for installation within the demanding operating conditions and hazardous areas of process plants. It enables a direct connection of field devices to Ethernet-based systems in a way that process industries can benefit from a convergence of their OT and IT systems. Utilizing a switched architecture, eliminates any unwanted interference between devices connected to the same network.
Ethernet APL adopts technologies and options already established in the field of process automation. This includes the proven trunk-and-spur topology shown in the figure above with the ability to power up to 50 field devices with up to 500 mW each. Widely used and established cable infrastructures are specified to support the migration in brown field installations to Ethernet-APL.
The field switch provides point-to-point connections to the instrument. Field switches with fast Ethernet or Gigabit interfaces support redundancy of the infrastructure with parallel redundancy, the media redundancy protocol, (MRP) or device level ring (DLR). The switches are easily configured for redundant logical connections since the data just passes through the infrastructure, e.g. an instrument can maintain multiple communications paths to controllers to enable controller redundancy.
Likely! The cable must be shielded for reliable communication. The reference cable is type ‘A’, which is widely used in process industries, e.g. in fieldbus installations. Many users can re-use this installed cable base. Because of the higher frequency range, which is not explicitly specified for most cable installed today, the experts highly recommend testing the installed cable. This is even more important if shielded cable other than type ‘A’ is considered for re-use. A reduction in usable cable length should be expected. For conformance information, refer to the Ethernet-APL engineering guideline.
Ethernet APL definitions enable application and installation in any hazardous area. The possible installation of field devices and field switches depends on the manufacturer’s design of the product and is not related to Ethernet-APL technology. The new intrinsic safety concept for the Ethernet-APL spurs, called 2-WISE (2-Wire Intrinsically Safe Ethernet, IEC TS 60079-47) and the port profiles allow for intrinsically safe circuits corresponding to “ia” type of protection – which is suitable even for Zone 0, Zone 20 or DIV 1 installations.
Reduced Time-to-Market and Simplified R&D
Product manufacturers and software vendors face a challenge to efficiently integrate industrial communication protocols and data exchange standards into their products. Communication subsystems consisting of protocol stacks, hardware base and application interface are a critical layer of technology, but they hardly differentiate a product or solution they are integrated into. At the same time, these protocols and functions are hard to implement and to maintain, and they require scarce technology expertise to do so.
Hence there is a clear case for product manufacturers and software vendors not to develop industrial communication protocols in-house, but to integrate communication technology available as off-the-shelf products, such as software stacks, software development kits (SDKs) or modules. Users benefit from reduced time-to-market, simplified, more efficient development, and significant cost savings.
Ethernet-APL – the New Gold Standard for Process Automation
Ethernet-APL Offers Benefits for Both End Users and Device Manufacturers
Ethernet-APL (Advanced Physical Layer) is a two-wire Ethernet physical layer using 10BASE-T1L as defined by IEEE 802.3cg, which is equipped with additional provisions for process manufacturing and therefore forms part of the IEEE 802.3 Ethernet specification. For networks in the process industry, this new technology offers full interoperability and flexibility, thanks to seamless field device connectivity via the Ethernet protocol coupled with rapid data transmission on the information layer across large distances, plus the supply of power to field devices. As a result, modern, fast and high-performance automation networks can now be set up much more easily as part of digital transformation projects.
Getting Started With Ethernet-APL
For end users, Ethernet-APL creates new layout opportunities when building high-performance automation networks. As mentioned, this means field devices can be integrated seamlessly into the network via Ethernet – and we’re not talking about a few pieces of equipment devices but millions of installed devices, such as small sensors, control units, or highly complex analytical instruments. Every year, a similar volume of new devices is added, with most of these still using 4–20 mA technology, potentially supplemented by digital point-to-point communication over the HART protocol. This is supplemented by the many – now legacy – digital field buses for transmitting additional measurement data and parameters still present in many installations. However, this latter scenario is reserved for specialized applications only due to the complexity, costs and specific gateway components and expertise that are required.
Ethernet-APL as the New Standard for Cost-Effective Networks in the Process Industry
Formally adopted in 2021, Ethernet-APL is a new standard for end-to-end Ethernet communication right down to individual field devices. The standard accounts for the specific requirements of the process industry, like the bridging of large distances with a simple, two-wire conductor that not only handles data communications but also supplies power to the connected field device. Another significant step was taken by increasing transmission rates to 10 Mbps compared to HART and field buses. APL also limits itself to defining a new data exchange standard for Ethernet at the lowest layer, ensuring that it retains compatibility with any Ethernet-based protocols at higher layers. For the first time, this makes transparent communication possible between production and company networks down to field devices, while removing the need for expensive gateways. Automation protocols can be deployed as required, as can web servers, OPC UA, and cloud/edge connectivity.
How Can Lead Times be Minimized for End Users and Device Manufacturers?

The Ethernet-APL Engineering Guideline describes three separate network topologies for Ethernet-APL networks. In terms of network topology, however, we at Softing assume that network operators will prefer an alternative where an APL field switch is integrated directly into the control network. With this in mind, Softing has developed an aplSwitch product line that supports both copper- and fiber-based connectivity, and will be launched by the end of 2023. Netload rate limits, which are supported by all of Softing’s APL switches, help to ensure optimum network stability. How does netload rate limiting work? To keep a PROFINET network running stably, it is important to monitor the network load that Ethernet-APL devices are subjected to. Where networks transition from 100 Mbps to 10 Mbps, a higher network load in the 100 Mbps control network is especially critical for the Ethernet-APL devices on the 10 Mbps spurs, because their data throughput is only 10 percent of that of the control network. This means that the ingress and egress data traffic at switch ports needs to be limited by setting netload rate limits. Softing is also working on designing other, optimized APL switch variants for installation directly in the field and the enclosure.

As we see it, device manufacturers should avoid having to start development projects from scratch by opting for a redesign that utilizes an electronics module providing all of the hardware and software components needed for communications. This is the only way to implement new Ethernet-APL-compatible devices within a short time-to-market. Softing supports manufacturers who are facing this very challenge with its new commModule APL which is a low-cost SMD hardware module. Supplied with a pre-installed PROFINET stack, commModule APL offers a configurable application data model as well as command mapping that can be used to migrate existing HART and Modbus devices to Ethernet-APL without a single line of code having to be written. Assignments to HART or Modbus commands are made using the corresponding commScripter tool. commModule APL has already completed extensive EMC and environmental testing, as well as conformance testing for the Ethernet-APL physical layer and the PROFINET protocol with PA Profile 4.02. The module has also been pre-certified to the ATEX and IECEx standards. All of these properties help to drastically reduce the effort and time investments that need to be considered when developing device hardware from scratch.
The Advantages of Softing’s Ethernet APL Solutions at a Glance

Ethernet APL Brings Flexibility and Future-Proof Network Structures
Ethernet-APL offers a wealth of flexibility and options for individual network structures and a level of maturity permitting the deployment of corresponding devices in production environments. It has other obvious benefits too as it avoids hardware costs, no dedicated gateway components need to be purchased and no expert-level configuration tasks are required in particular to integrate with the upstream Ethernet infrastructure of the equipment responsible for these gateways. An implementation should nonetheless be planned and structured properly in order to exploit all the advantages of this new standard – and Ethernet-APL should certainly be considered as a candidate for any future planning work.
Thinking about deploying Ethernet-APL?